Selective Conformal Coating for High-Reliability Electronics: Quality Control Insights
- VAJRA
- Mar 11
- 3 min read
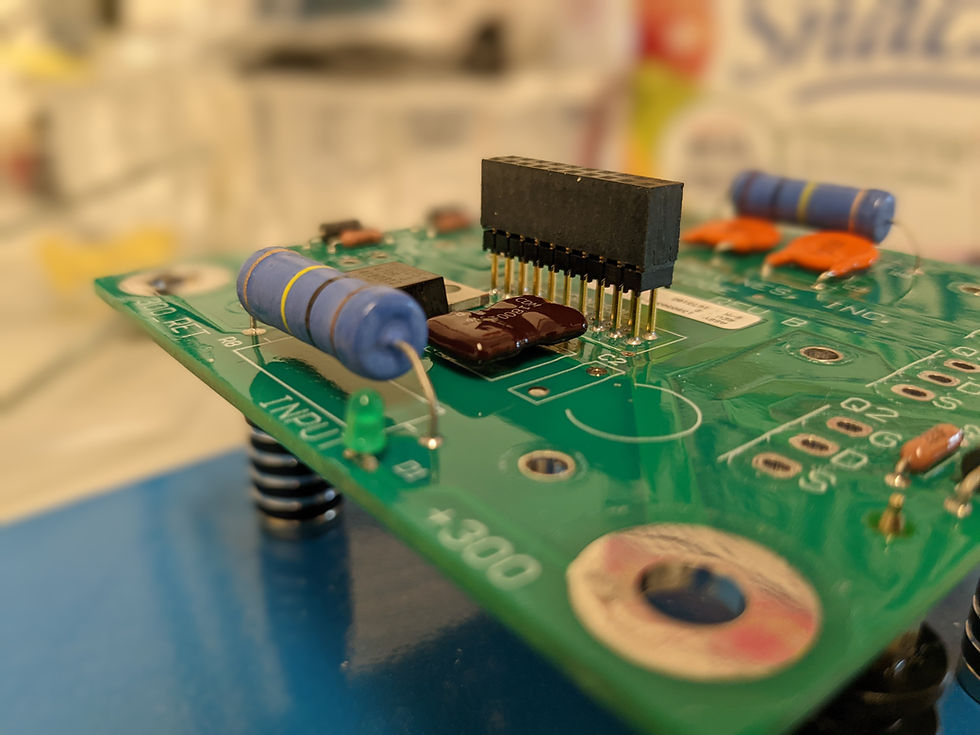
Selective conformal coating plays a vital role in protecting high-reliability electronic assemblies from harsh environmental conditions. It enhances product durability in industries such as aerospace, medical, and RF/microwave electronics. However, achieving consistent quality in selective conformal coating requires strict adherence to quality control measures, precise inspection techniques, and effective rework strategies. This article explores key quality control insights, inspection techniques, and rework challenges in selective conformal coating processes.
1. Importance of Quality Control in Selective Conformal Coating
Quality control in selective conformal coating ensures reliability, durability, and compliance with industry standards. Defects in coating application can lead to electrical failures, corrosion, or signal integrity issues in sensitive electronic devices.
Key Quality Control Objectives
Uniform Coating Thickness – Prevents performance degradation due to over- or under-coating.
Proper Adhesion – Ensures coating firmly adheres to the substrate, reducing delamination risks.
Full Coverage of Critical Areas – Protects against moisture ingress while avoiding unintended areas such as connectors and test points.
Minimal Voids and Bubbles – Ensures coating consistency without defects that can compromise protection.
Compliance with Industry Standards – Guarantees products meet regulatory and safety requirements.
2. Inspection Techniques for Quality Assurance
Inspection is a critical step in verifying that selective conformal coating meets specifications. Various methods help detect defects such as delamination, voids, bubbles, contamination, and uneven coverage.
2.1 Visual Inspection
Process:
Performed under white or UV light to detect coating presence, thickness, and uniformity.
Helps identify defects such as missing areas, pooling, and contamination.
UV fluorescence in coatings allows quick defect detection in dim light conditions.
Best Practices:
Use magnification tools (5x-10x) for a detailed inspection.
Check masking areas to ensure no unintended coating migration.
Verify coverage on sharp edges and high-profile components.
2.2 Automated Optical Inspection (AOI)
Process:
High-speed AOI systems capture high-resolution images of coated PCBs.
Compares applied coating with the expected design to detect inconsistencies.
Advantages:
Reduces manual errors and speeds up defect identification.
Ideal for high-volume production lines.
2.3 Cross-Sectional Analysis
Process:
Involves slicing through a coated PCB to examine layer adhesion and thickness.
Used for failure analysis and process optimization.
Applications:
Helps analyze defects such as voids or delamination not visible through surface inspection.
Provides detailed insight into coating integrity over time.
2.4 Thickness Measurement
Techniques:
Wet Film Gauges – Measure thickness before curing.
Micrometers and Calipers – Measure cured film thickness in non-critical areas.
Ultrasonic Thickness Testing – Non-destructive method ideal for multi-layered coatings.
Recommended Tolerances:
Acrylics & Polyurethanes: 25-75 microns
Parylene: 10-25 microns
Silicone: 50-200 microns
2.5 Electrical Testing
Process:
Verifies coating insulation properties by measuring resistance and dielectric strength.
Helps ensure coating does not interfere with circuit performance.
Common Tests:
Dielectric Withstand Testing (Hi-Pot Test)
Insulation Resistance Testing
3. Rework Challenges and Best Practices
Reworking conformal coating presents unique challenges due to adhesion strength, reflow resistance, and material properties. Careful planning is required to ensure minimal damage to electronic components.
3.1 Common Rework Challenges
Coating Removal without Damaging Components – Some coatings, such as parylene, require specialized removal techniques.
Avoiding Mechanical Stress on PCB – Scraping or excessive heating can damage delicate circuits.
Ensuring Complete Removal Before Reapplication – Residual material can lead to adhesion failures.
Masking and Precision Application During Rework – Reapplying coating in a controlled manner can be difficult, especially for localized repairs.
3.2 Rework Techniques
Solvent-Based Removal
Used for acrylic and polyurethane coatings.
Common solvents: Acetone, Toluene, and MEK.
Must be used with proper ventilation and PPE.
Thermal Removal
Effective for silicone and urethane coatings.
Uses controlled heat (100-200°C) to soften and peel off the coating.
Micro-Abrasive Blasting
Removes coatings via fine particle blasting (e.g., sodium bicarbonate or aluminum oxide).
Best for localized coating removal without affecting nearby components.
Laser Ablation
A precise and controlled method for removing coatings layer by layer.
Ideal for high-reliability applications where minimal damage is critical.
Mechanical Scraping & Peeling
Suitable for thin coatings but requires care to avoid PCB damage.
Often combined with solvent softening to ease removal.
3.3 Best Practices for Rework
Evaluate Coating Type Before Choosing a Removal Method – Different coatings require different techniques.
Use Minimal Force to Prevent Damage – Avoid excessive scraping or aggressive cleaning.
Thoroughly Clean and Prepare Surface Before Reapplication – Ensures new coating adheres properly.
Test Reworked Areas to Verify Coating Integrity – Use UV inspection, adhesion testing, and electrical tests.
Implement Process Controls for Rework Consistency – Standardized procedures reduce variability in rework quality.
Conclusion
Selective conformal coating is essential for ensuring the reliability of electronic assemblies in harsh environments. Implementing robust quality control practices—ranging from visual and automated inspection to thickness measurements and electrical testing—helps minimize defects and improve product reliability.
However, rework remains a challenge due to adhesion properties and removal complexities. Selecting the right removal technique, ensuring proper surface preparation, and maintaining consistent reapplication are crucial to minimizing failures and maintaining performance.
Comments